29 Jul Quality Assurance vs Quality Control
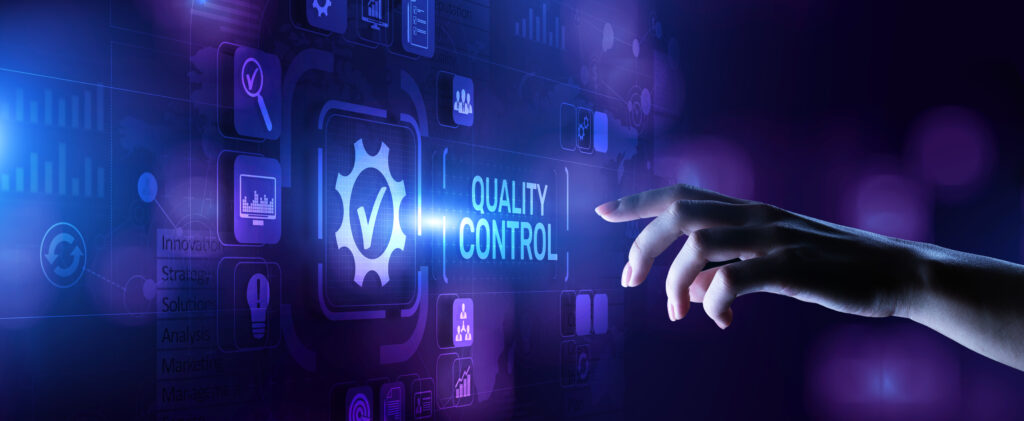
Quality Assurance vs Quality Control
In the medical device industry, ensuring the safety and effectiveness of products is paramount. This is achieved through two critical functions: Quality Assurance (QA) and Quality Control (QC). Although these terms are often used interchangeably, they refer to distinct processes that play unique roles in the overall quality management system (QMS). Understanding the differences between QA and QC is essential for maintaining high standards such as ISO 13485 and regulatory compliance.
Quality Assurance (QA)
Quality Assurance is a proactive, process-oriented approach aimed at preventing defects in the manufacturing process. It involves continuous monitoring and improvement of processes to ensure that they meet predefined standards and regulatory requirements.
Key Aspects of Quality Assurance:
- Process Focus: QA emphasizes the manufacturing process, ensuring that every step is performed correctly to prevent defects.
- Proactive Measures: QA involves planning and implementing processes to avoid issues before they occur.
- Continuous Improvement: The PDCA (Plan-Do-Check-Act) cycle is commonly used in QA to continuously improve processes.
- Regulatory Compliance: QA ensures that all processes comply with regulatory standards such as those set by the FDA, ISO, and others.
Common QA Activities:
- Audits: Regular inspections to ensure compliance with internal and external standards.
- Process Definitions: Detailed documentation of each process to ensure consistency and clarity.
- Tool Evaluation: Regular assessment and calibration of tools and equipment used in manufacturing.
- Training: Ongoing training for staff to ensure they are knowledgeable about QA processes and standards.
Processes and SOP’s for QA’s in the Medical Device Industry
We provide a bunch of helpful documents and articles related to processes and SOP’s in the medical device industry. In the following article you will find detailed information about required processes related to ISO 13485, EU MDR 2017/745 and EU IVDR 2017/746. CLICK HERE
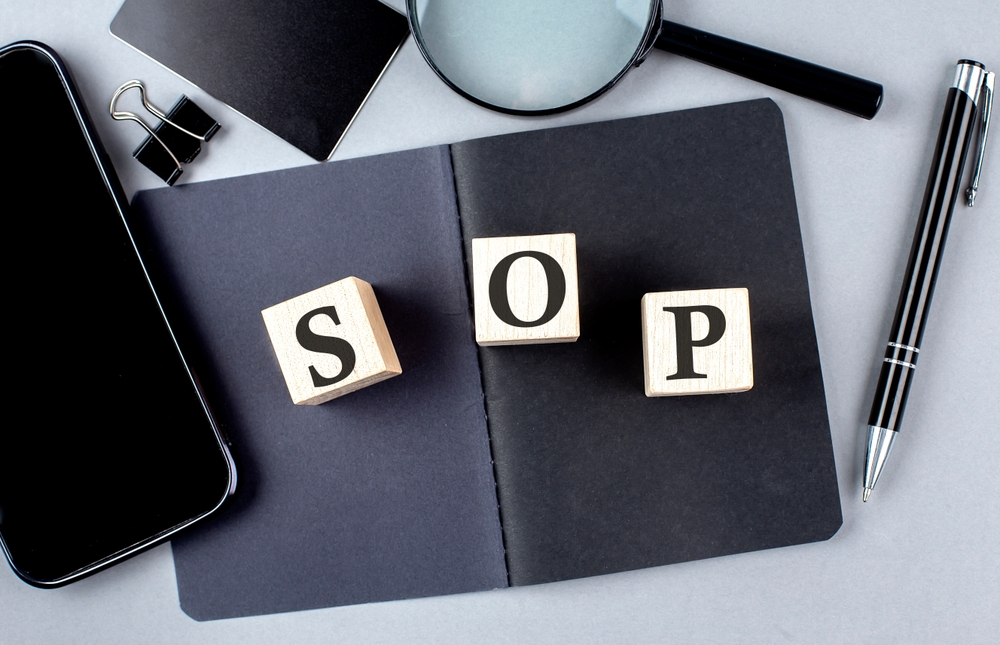
Quality Control (QC)
Quality Control is a reactive, product-oriented approach that focuses on identifying defects in the final product. It involves testing and inspection of products to ensure they meet the required specifications before they are released to the market.
Key Aspects of Quality Control:
- Product Focus: QC emphasizes the final product, ensuring it meets all specifications and standards.
- Reactive Measures: QC identifies and addresses defects after the product has been manufactured.
- Testing and Inspection: QC involves rigorous testing and inspection to catch any defects before products reach the end-user.
- Corrective Actions: When defects are found, QC teams initiate corrective and preventive actions (CAPA) to address the root cause and prevent recurrence.
Common QC Activities:
- Acceptance Criteria: Establishing and documenting criteria for product acceptance.
- Product Testing: Conducting tests to verify that products meet the required specifications.
- CAPA Management: Investigating nonconforming products and implementing corrective actions.
10 Key differences between Quality Assurance vs Quality Control
This table shows the main essential differences between QA and QC:
Aspects | QA | QC |
Focus | Proactive, preventing defects through process management | Reactive, detecting and correcting defects in products |
Objective | Process-oriented, improving and stabilizing production processes | Product-oriented, identifying defects in finished products |
Timing | Throughout the production process | At the end of the production process |
Nature of Activities | Process planning, documentation, training, continuous improvement | Inspection, testing, defect identification and correction |
Responsibility | Involves everyone in the organization | Primarily involves inspectors and QC personnel |
Approach | Preventive, aiming to improve processes | Corrective, identifying and fixing defects |
Goal | Establish procedures to ensure consistent quality standards | Verify products meet specified standards before release |
Impact | Long-term impact on production processes | Immediate impact on specific products or batches |
Inspection Focus | Processes and system adherence | Final product examination for defects |
Tools and Techniques | Process mapping, quality audits, training | Statistical process control, inspection techniques |
.
These differences highlight the distinct roles that QA and QC play in ensuring the overall quality of products and services.
Integration of QA and QC with Elly
Using AI in the QA and QC area can be and will be the next big step to increase quality in your business overall. We at Regulatory Globe creating such advanced tools as Elly, our AI-driven regulatory affairs assistant can help to enhance both QA and QC activities. Elly is trained on medical device and in vitro diagnostic regulations globally and can provide comprehensive support in ensuring compliance and quality in the medical device industry.
Conclusion
Understanding the distinction between Quality Assurance and Quality Control is crucial for maintaining high standards in the medical device industry. While Quality Assurance focuses on preventing defects through process optimization, Quality Control ensures that the final product is free from defects. By integrating advanced tools like Elly, companies can enhance their QA and QC efforts, ensuring the delivery of safe and effective medical devices.
Regulatory Intelligence Service:
We are helping companies with being up to date with medical device regulation globally. Learn more and join our exclusive service by clicking HERE.
No Comments