04 Aug SOP
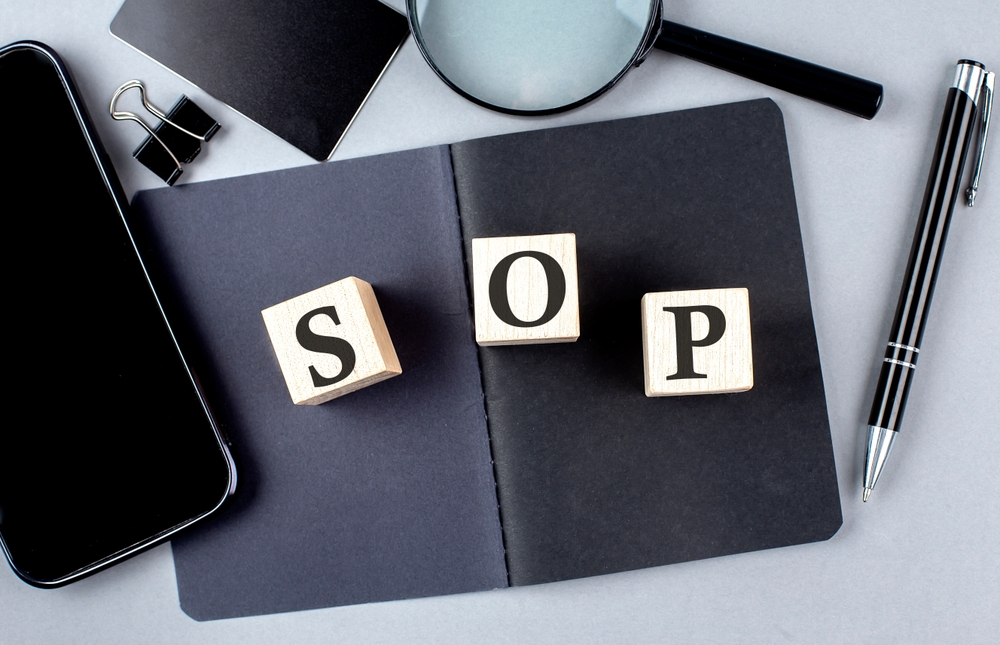
SOP (Standard Operation Process)
In the highly regulated medical device industry, processes and SOP’s (Standard Operating Procedures) are indispensable. They help to increase quality and consistency in the development and production of products like Medical Devices. The main regulations and standards in this area are ISO 13485, QSR 21 CFR 820, and the new QMSR. This article will delve into the importance of processes and SOP’s that are required, providing a list of such important processes and SOP’s, how to craft them and best practices for maintaining them.
What are SOP’s?
SOPs are detailed, written instructions designed to achieve uniformity in the performance of specific functions. In the medical device field, SOPs cover various aspects including design controls, manufacturing processes, risk management, and quality assurance.
Differences Between SOPs and Processes
Understanding the distinction between SOP’s and processes is crucial. Both play integral roles in ensuring consistency, quality, and regulatory compliance, but they serve different purposes and operate at different levels of detail.
Level of Detail
Processes are high-level descriptions that outline the sequence of activities transforming inputs into outputs. They provide a broad overview of what needs to be done and why, often encompassing multiple steps and interactions. For example, a manufacturing process might include steps such as material procurement, assembly, quality control, and packaging.
In contrast, SOPs are detailed, step-by-step instructions for carrying out specific tasks within those broader processes. They are designed to ensure that each task is performed consistently and correctly every time. An SOP for the quality control step in the manufacturing process might detail the exact procedures for inspecting and testing products, including the specific tools and criteria to be used.
Importance of SOP’s in the Medical Device Industry
- Regulatory Compliance: SOPs help companies comply with regulatory requirements, reducing the risk of non-compliance penalties.
- Consistency and Quality: They ensure that every task is performed consistently, leading to high-quality products.
- Training and Onboarding: SOPs serve as training material for new employees, ensuring they understand and follow established procedures.
- Operational Efficiency: Well-documented SOPs streamline operations, reducing errors and improving productivity.
Relevant Processes and SOP’s according to ISO 13485, QSR and QMSR
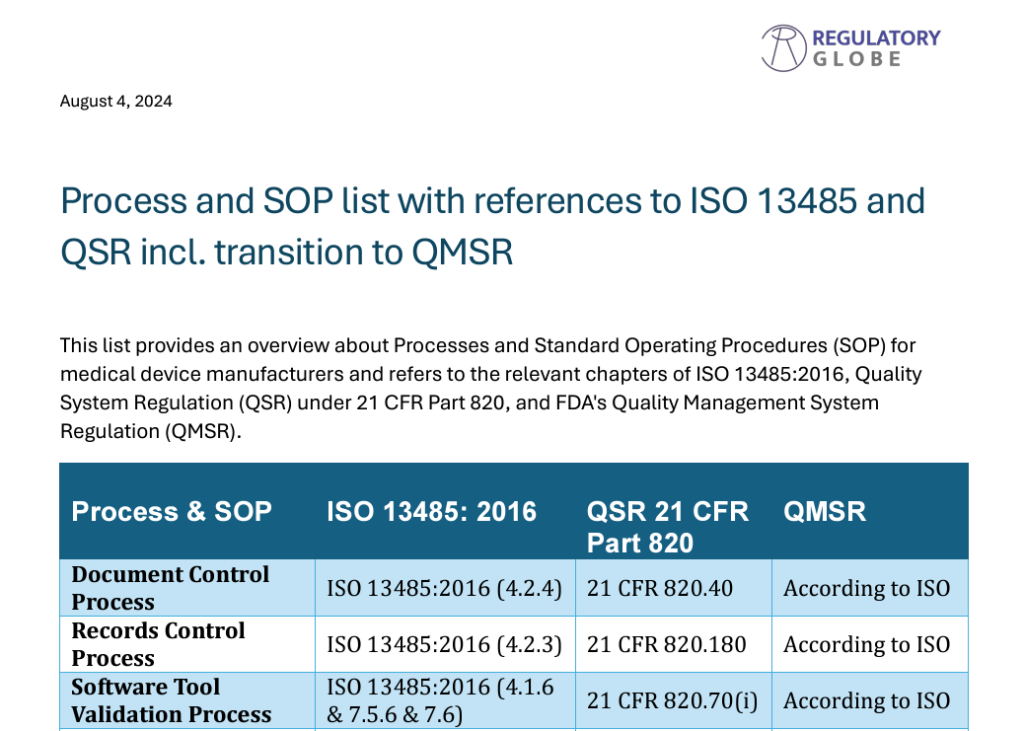
Relevant SOP’s and Processes according to EU MDR and EU IVDR
Processes and SOP’s by EU MDR and EU IVDR:
EU MDR and IVDR Required Procedures and Processes: | Reference in EU MDR: | Reference in EU IVDR: |
Clinical Evaluation Procedure | Article 61, Annex XIV | Article 56, Annex XIII |
Clinical Evaluation Consultation Procedure (For certain Class IIb and III products) | Article 54, Annex IX | N/A |
Performance Evaluation Procedure | N/A | Article 56, Annex XIII |
Post-market Surveillance Process | Article 83, Annex III | Article 78, Annex III |
Post-market Clinical Follow-up Process | Article 61, Annex XIV | Article 56, Annex XIII |
Regulatory Affairs Procedure | General provisions throughout the MDR | General provisions throughout the IVDR |
Identification of Applicable Regulatory Requirements Procedure | General provisions throughout the MDR | General provisions throughout the IVDR |
Performance Evaluation Process | Annex XIII – Part A – Performance Evaluation and Performance Studies | Annex XIII: Performance evaluation, performance studies and post-market performance follow-up |
Post-market Performance Follow-up Process | N/A | Annex XIII: Performance evaluation, performance studies and post-market performance follow-up |
Customer-made Devices Procedure | Annex XIII | N/A |
System and Procedure Pack Assembly Procedure | Article 22 | Article 22 |
Traceability and UDI Storage Procedure | Article 27, Annex VI | Article 24, Annex VI |
Best Practices for Writing SOP’s
- Plan Thoroughly: Before drafting an SOP, plan its structure and content. Identify the purpose of the SOP, the tasks it will cover, and the intended audience.
- Engage Stakeholders: Involve employees who will use the SOP in the drafting process. Their input can help make the SOP more practical and user-friendly.
- Review and Revise: Regularly review and update SOPs to ensure they remain relevant and effective. Incorporate feedback from users and changes in regulations or processes.
- Train Employees: Conduct training sessions to ensure all employees understand and can follow the SOPs. Use quizzes and practical assessments to verify understanding.
- Document Control: Implement a document control system to manage SOP versions, revisions, and approvals. This ensures that only the most current SOPs are in use.
Common Pitfalls and How to Avoid Them
- Overly Complex Language: Use simple, clear language to ensure the SOP is understandable to all employees.
- Lack of Detail: Provide sufficient detail to avoid ambiguity. Include all necessary steps and precautions.
- Infrequent Updates: Regularly review and update SOPs to reflect changes in processes, technology, or regulations.
- Poor Training: Ensure that all employees are adequately trained on new and revised SOPs. Use practical assessments to verify their understanding.
Conclusion
SOP’s are the backbone of quality and compliance in the medical device industry. By using a well-structured SOP’s and following best practices, companies can ensure their SOP’s are effective, user-friendly, and compliant with regulatory standards. Regular updates and thorough training are essential to maintaining the relevance and effectiveness of SOP’s.
Regulatory Intelligence Service:
We are helping companies with being up to date with medical device regulation globally. Learn more and join our exclusive service by clicking HERE.
No Comments